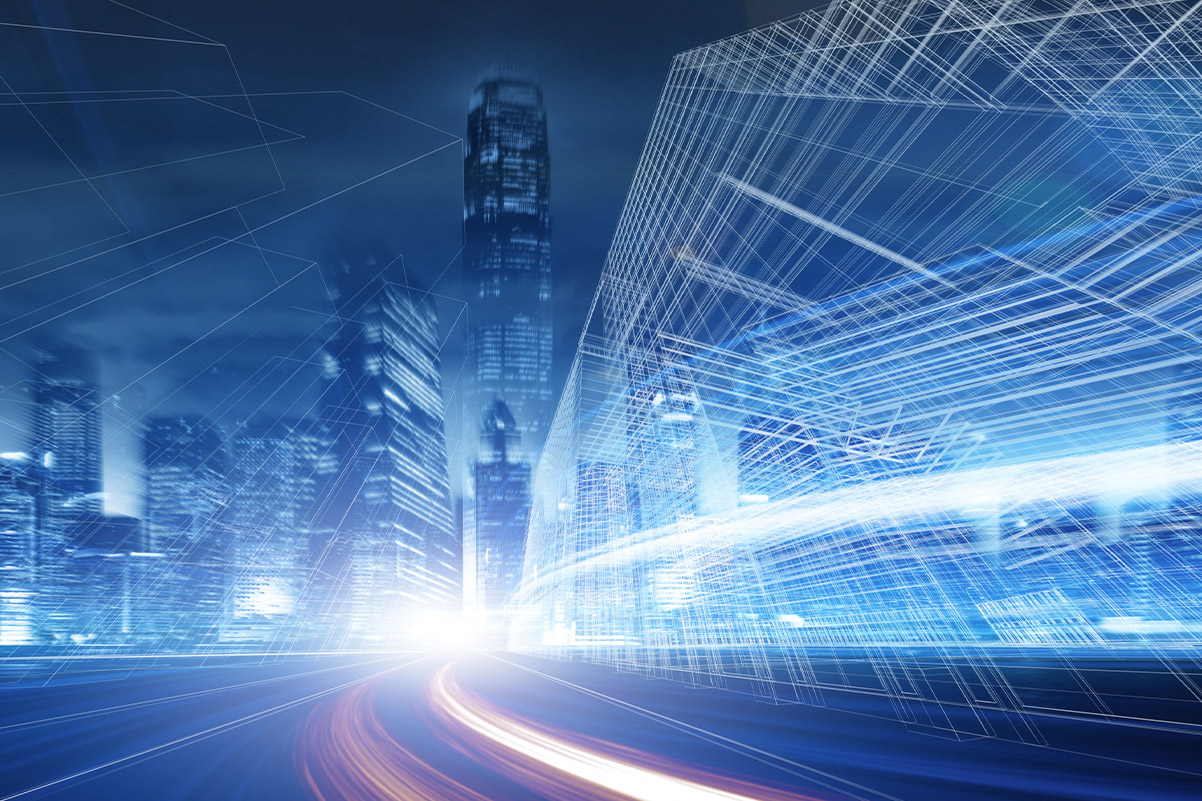
In 2015, China’s Broad Sustainable Building (BSB) company built a 57-story high rise in just 19 days. If you do the math, that averages three floors every day. The building housed 800 apartments, 19 atriums and office space for 4,000 workers. While this feat is truly incredible, the thinking behind it has been around for a long time. Prefabrication seen many iterations over the decades, but the construction industry has finally adopted it on a large scale.
Change is not a common phenomenon in the construction industry which hasn’t seen a major shake up in over four decades. While other industries automated and turned to the manufacturing process to increase productivity, the construction industry languished on jobsites across the world. That is all about to change and your next project won’t be built, it will be manufactured.
“Although all of this was a unique idea 10 years ago, almost every major design school is now teaching the fundamentals of prefab,” says Phil Bernstein, keynote speaker at the 2019 IWBCC conference. “A new generation is coming into the field equipped to do this, and the wheels of manufacturing buildings will soon be humming. Those folks will catch the wave of prefabrication fully, and workers swinging hammers will give way to assemblers in the era of manufactured buildings.”
Why Now?
If the construction industry is resistant to change, why this sudden adoption of new techniques? Prefabricated architecture has been around for a long time, but the perfect storm of circumstances is pushing it mainstream. An increased use of digital models and fabrication methods as well as revolutionary techniques such as additive manufacturing, 3D printing, robotics and CNC-controlled technologies and laser scanning are changing the way designers and construction professionals are able to create.
Advances in technology and economic factors such as labor shortages have culminated in change. During the last recession, millions of construction workers left the industry, never to return. Coupled with more stringent immigration policies, the well of construction workers has dried up and they are no longer able to support a growing industry. With baby boomers retiring, skilled workers are in short supply.
Thanks to technological and robotic breakthroughs, a lack of skilled labor and an aging workforce and rising labor costs, prefab is offering a cheaper, more sustainable option for developers.
The Road to Offsite Building
With prefabricated building, design plays a major role. Designers are able to optimize the functionality of buildings while having more freedom to create bespoke structural elements. Building components will be built offsite and then snapped into place. This saves time in construction, eliminates the weather as a factor and utilizes fewer skilled workers.
Prefabrication doesn’t mean mass production of generic ‘cookie cutter’ buildings that all look the same. Once prefabrication is mainstream, mass customization will follow.
Where are we at?
As designers and manufacturing facilities work to catch up, it’s inevitable that teething problems occur. For example, 2018 saw Brooklyn’s Pacific Park (formerly named Atlantic Yards) project grind to a halt. It was set to be the world’s tallest modular-constructed building, but challenges in the design and fabrication caused the project to falter.
Prefabricated construction is a disruption of an industry steeped in tradition. This kind of major change always creates some chaos as transition occurs. As each element of the construction industry evolves to meet the new challenge, the nature of the work and the roles professionals play will change too.
As we look to the future, the only thing we can be sure of is that the construction industry will be forever changed.